Panaro MAX® cases: Industry’s First to disclose CO2 impact of industrial cases with Pickler.
Panaro MAX® cases became their industry's first to measure and disclose the CO2 impact of industrial cases with Pickler. This is how.
By
Zazala Quist
On
February 22, 2024
Key insights
1. Impact Widgets showcasing environmental impact for every product on MAX® cases website
2. Designed the EKO-case: 100% recycled materials used
3. Educating users on end-of-life challenges
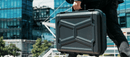
Company snapshot
- Drones, Defense, Machinery and more
- The Netherlands
- Industrial cases
- https://www.maxcases.nl/
Longing for change - turned into action
Panaro noticed a lack of sustainability trends, demands or sector-specific rules in their market.
So - what motivates a market to change? Someone who sets a new status quo.
“Our specific industry is quite late to embracing sustainable developments. There’s a heavy focus on long product life, quality, and durability. All logical aspects of course, as this is the core purpose of our type of packaging. However, environmental impact and sustainable material use are only recently introduced concepts, not yet turned into trends. We thought; well - it’s time someone starts”
- Jan Peter Ruis, CEO at Panaro Services
Sustainable awareness based on proof
Panaro thought it was about time to make quality and sustainability equal. Their goal: make product impact transparancy the new status quo in the traditional industry.
But where do you start? As a manufacturer, they knew their biggest chunk of impact would come from their products.
So, they wanted insights into the footprint of their cases first - to start their sustainability journey.
Their dream journey:
- Educate themselves on where their impact comes from.
- Test sustainable product improvements.
- Be the first in the market to disclose CO2 data to customers.
The only problem: they struggled to find an easy, affordable way to do so. Especially since they lack a lot of supplier data on the materials they purchase for their manufacturing processes.
Until they found Pickler.
Why Pickler?
Panaro became one of Pickler’s first customers. Due to Pickler’s comprehensive database of packaging materials and its user-friendliness, they could start right away.
Why Pickler:
- The simplicity: Pickler was made to get packaging companies start calculating and sharing the footprint of theior packaging within minutes. Even with gaps in supplier data.
- Continuously updated results: Working with Pickler isn’t a one-off stop. Footprint results are updated with better impact information and new electricity mixes due to the auto-updated impact database. Something that’s required by the EU’s Green Claims Directive. Changes in material use or improvements can be made at any time. Ensuring credible always accessible footprint results.
- Packaging focus: Panaro wasn’t looking for a company footprint certificate or eco-label, etc. But a tool that would give them detailed insights into the footprint of their products. Even better: a tool that’s focused on packaging products specifically.
“When I first signed up for Pickler, I instantly grasped its value - making my first calculations within minutes already. It’s so easy. You immediately see where your product’s biggest impact comes from and can compare these so-called hotspots to sustainable alternatives. This helps us understand and make sustainable product improvements. A solution we were looking for, for a very long time already.”
- Jan Peter Ruis, CEO at Panaro Services
How do you measure the footprint of packaging?
Pickler calculates the environmental footprint of packaging using our scientific LCA-based Pickler methodology and the IDEMAT database. These are compliant with ISO 14040, 14044, EN15804, and the LCA handbook of the ILCD. Ensuring the integrity and reliability of data used in Life Cycle Assessment (LCA).
The scientific method Life Cycle Assessment (LCA) calculates the environmental impact of every stage in your packaging's life cycle. From the production of its raw materials to producing the packaging itself, to transport distances, to its end-of-life. In LCA terms this scope is called cradle-to-grave.
No matter the number of products - Pickler connects your:
- product category
- product weight
- raw materials (BOM)
- production processes
- transport
- and end-of-life system;
- to average scientific impact data from its independent, auto-updated database Idemat.
The result: environmental scores and impact results (carbon footprint + 4 other impact categories) on your packaging. All ready to be shared with stakeholders.
Read everything about Picklers’ specific footprint results here.
1. Impact widgets for all products
Panaro made footprint calculations for all their products in Pickler. They share these results with customers in sales as well as on their website, via Pickler's impact widgets.
With Pickler's API, their Pickler results are linked to their website and constantly updated. This creates awareness of the impact of purchases - with a main focus on communicating their CO2-eq impact. Introducing evidence-based sustainability to their (potential) customers.
View the impact widgets on MAX® cases website here.
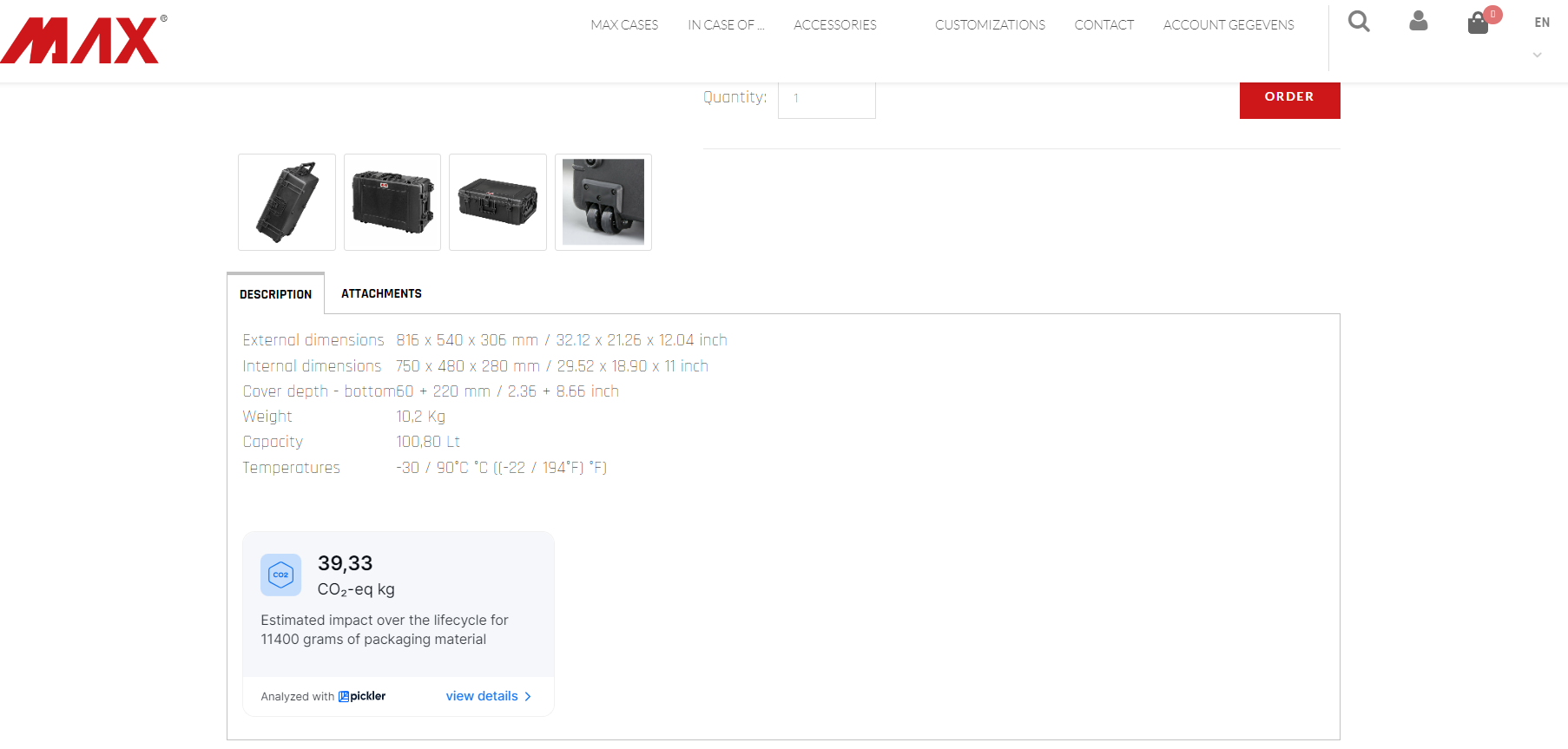
2. EKO-case: 100% recycled materials used.
Using Pickler’s comparison feature, they also tested different material scenarios to improve the footprint of their cases. The result: their EKO-cases, made of 100% recycled materials. And proof of the realized CO2 impact improvement with traditional cases to share with customers.
Offering a choice between:
- A case of 100 % recycled plastic with slightly less durability (due to the nature of recycled materials).
- A traditional case with primary materials and maximum durability.
Below you see the eco forecast of one of Panaro’s EKO cases, the EKO30. Find the full eco forecast for the Panaro EKO30 here.

3. Educating users on end-of-life challenges
Even though MAX® cases have a technical long lifetime (best scenario) and could be reused or recycled - they cannot control how clients will actually dispose of their cases.
The thing is: the end of life for cases is incineration - which isn’t great. Producing such a durable case costs a lot of emissions. The result is maximum protection and a possible product lifetime of 20 years. They also offer spare parts, to maximize their cases’ lifetime.
To reduce incineration, they educate customers how to best dispose of their cases and what the effects are if they don’t. Showing the two scenarios with Pickler’s comparison feature.
Panaros’ advice to customers:
- Return used cases to Panaro Services for reuse/recycling
- Reuse these cases yourselves
Next steps: Eco-design and awareness training
Panaro continues to use Pickler for:
1. Eco design: A design form where you test impact reduction over a product’s complete lifecycle impact. Think of testing material and transport improvements for their cases.
2. Awareness Training: They set up internal awareness sessions as well as footprint training for new team members and customers. These sessions and trainings cover how Pickler works and how employees and customers can use footprint data from the cases in their business. Slowly spreading awareness within a stubborn industry.
“The environmental impact data of our packaging within Pickler is constantly updated with the newest values and electricity mixes. Every change we want to test in terms of processes, transport distances, or materials - can be made and accessed 24/7. That’s the beauty of footprint software like this. We didn’t buy a one-off CO2 footprint value, we bought a sustainability solution.”
- Jan Peter Ruis, CEO at Panaro Services